Referent : Jean-Luc Maire
This theme aims to develop methods for optimizing processes in industrial companies. These may be production processes (manufacturing, but also research and development, design, delivery, etc.); support processes (control, maintenance, human resources, metrology, etc.); or even management processes (planning, continuous improvement, defining and monitoring objectives, etc.).
This optimization is part of digital transformation, i.e. the integration of digital technologies into all company activities. This digital transformation refers toIndustrie du Futur and more generally to Industrie 4.0 and even now (2024) to Industrie 5.0, which aims to enhance this digital transformation through the effective integration of people and technology, so that they work together more constructively in a secure environment.
Digital transformation is above all a question of business processes, not technology. The integration of new technologies requires companies to rethink the way they do things (practices, methods, business models, etc.), their skills (individual and collective) and, of necessity, their processes (implementation, support and management). It is on the basis of this observation that this research theme of the SYMME laboratory is structured.
Our research projects are linked to the various dimensions of digital transformation (Industry 4.0 / 5.0). More specifically, our aim is to provide answers and solutions to the following questions:
- on which processes should new technologies be integrated? What are the best practices for improving and optimizing operations? What progress approaches should be used, and how should they be managed?
- which digital technologies should be favored for a successful digital transformation?
- What type of organizational structure should be favored to support the digitization of processes? How can the roles of players within the organization be developed and/or created?
- what individual or collective skills need to be developed and mobilized to achieve optimum process performance? How can they be identified and effectively managed?
- what indicators characterize the company's adaptability to necessary changes in the academics offering?
- how can we change a company's culture so that it stimulates agility, change and innovation in process operations?
- Given that the above dimensions are interconnected, how do you define a process to manage the changes brought about by digital transformation in a coherent and effective way?
Some theme projects...
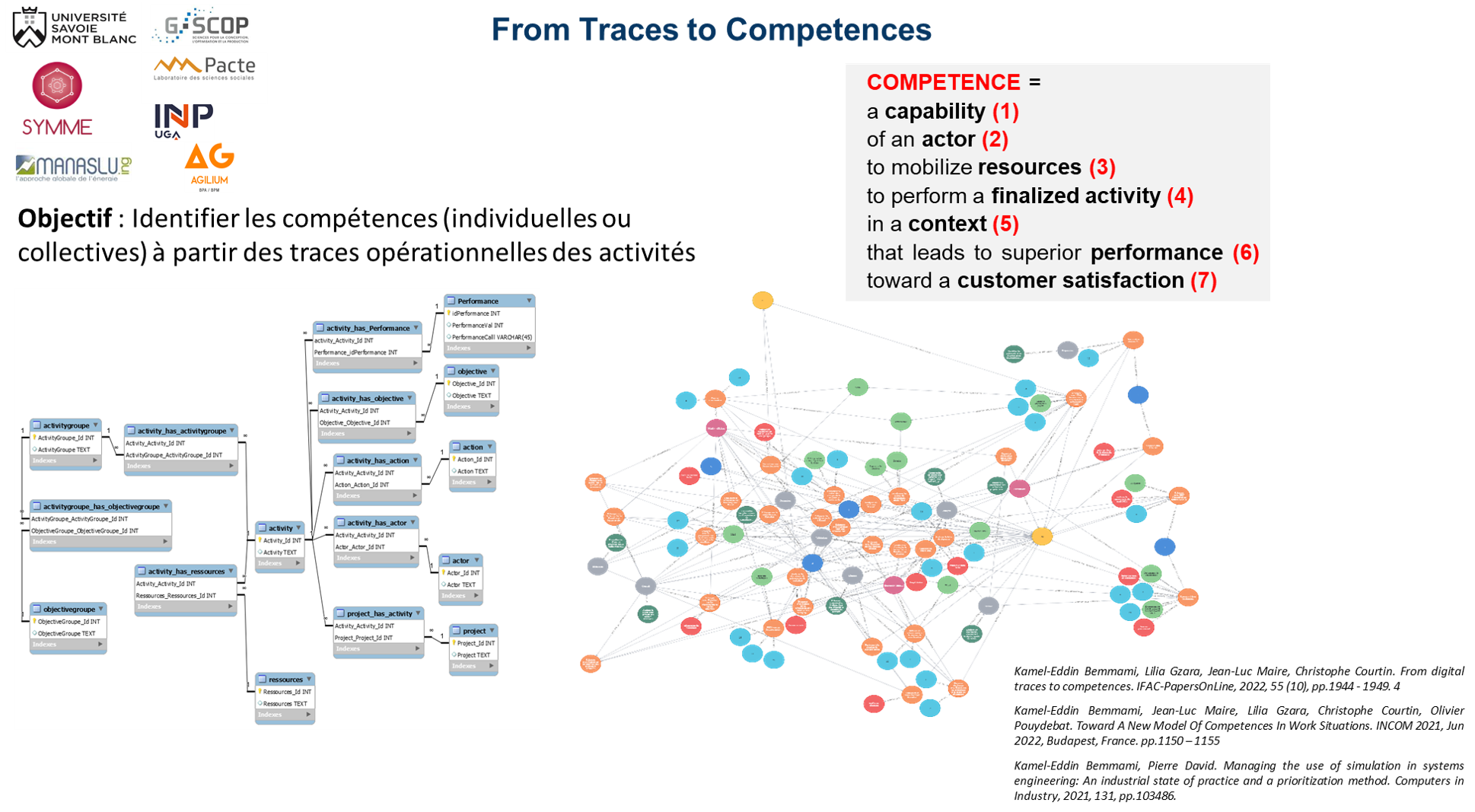
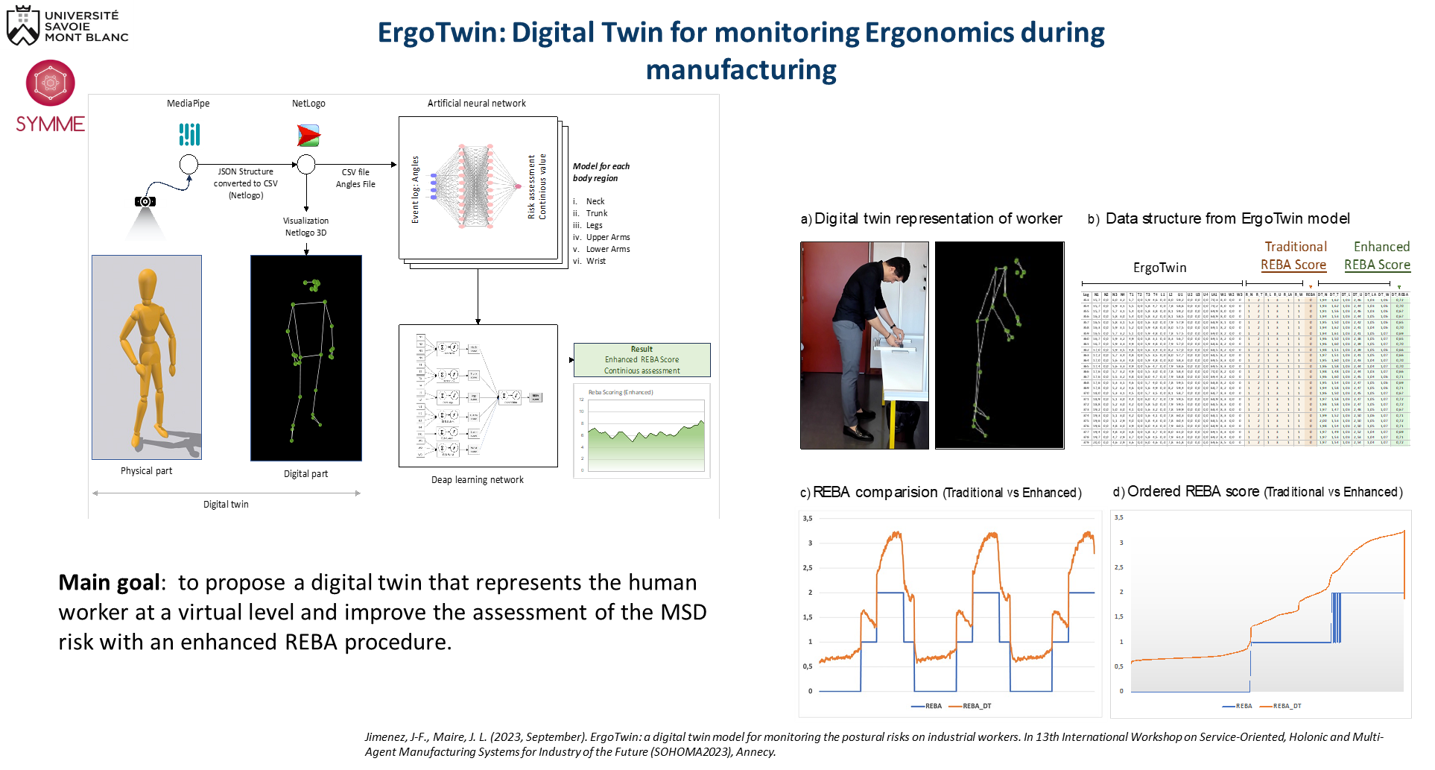
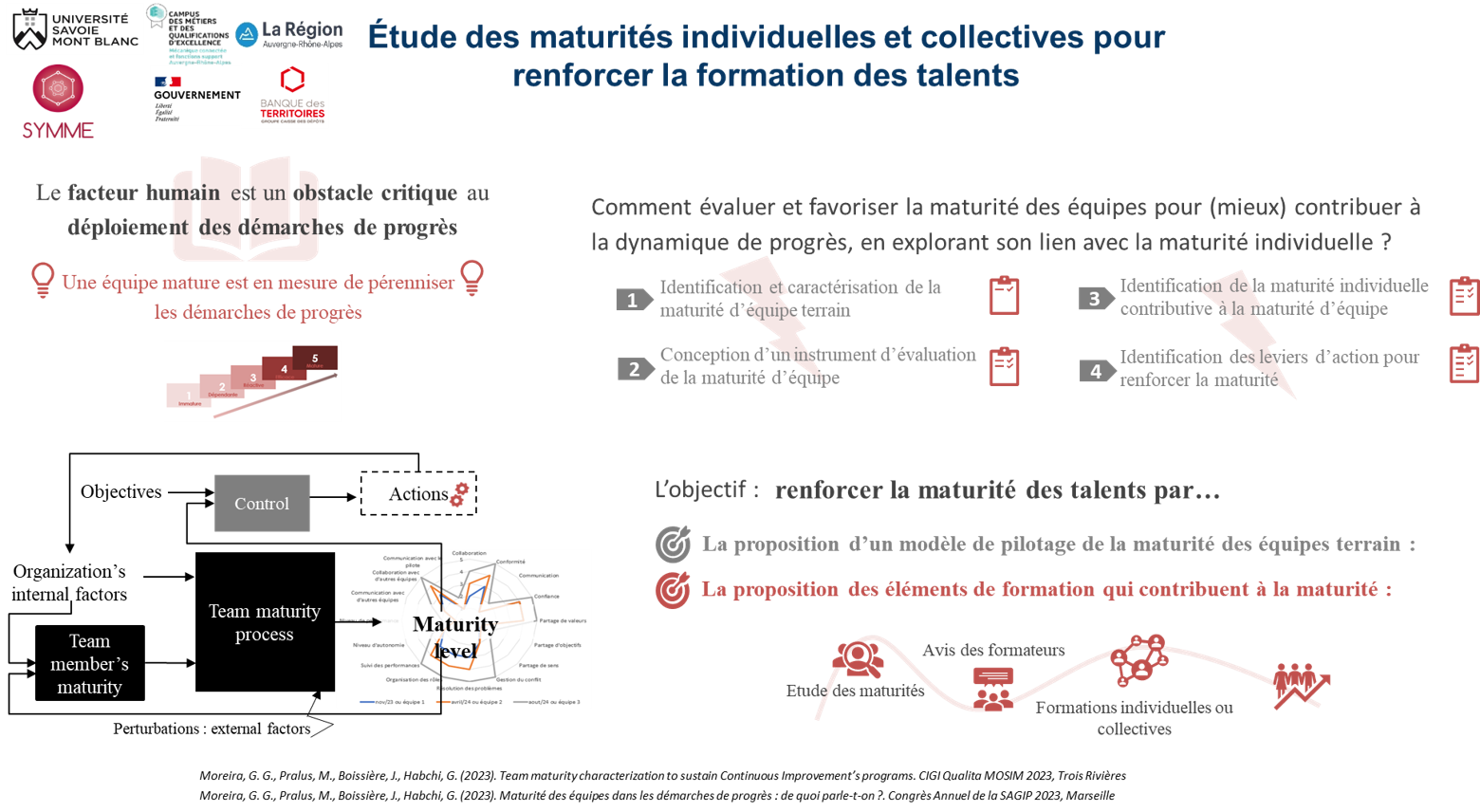